What is 3D Printing?
3D printing is based on a process of making three dimensional solid objects using computers. The object is created by interlaced layers of material such as liquid molecules or powder grains. Compared to traditional ways of manufacturing, 3D printing enables production of complex shaped goods using less material. Due to the precision, repeatability and wide range of supplies, 3D printing is defined as an industrial production technology, which is also called additive manufacturing.
Additive manufacturing requires CAD (computer aided design) software or 3D object scanners to deposit material in precise geometric shapes. Each successive layer bonds to the preceding layer formed from melted or partially melted material -like metal powder, thermoplastics, ceramics, glass and even chocolate-. As all the materials cool, they fuse together to form a three dimensional object. That’s how additive manufacturing works, basically.
Carbon Nanofiber
Carbon is the second most popular material after metal. When alone, carbon atoms are not useful as grouped together because it’s easy to break due to their thin, fragile nature. However, when they form a group and attach to each other, the fibers compose a very strong and light composite material.
Carbon Nano Fiber in 3D Printing
Today we have two methods of carbon nanofiber printing: chopped carbon nanofiber filled thermoplastic and continuous carbon nanofiber reinforcement. Both methods are using carbon nanofibers, but the difference between is huge. If we understand how they work and what the characteristics of them are, then we’ll be able to choose which fits in with our purpose. Chopped carbon nanofibers are printed through a standard printer and contain a thermoplastic reinforced with tiny chopped strands. Fabrication of continuous carbon nano fibers, however, is a different process that depends on continuous strands of carbon nanofiber.
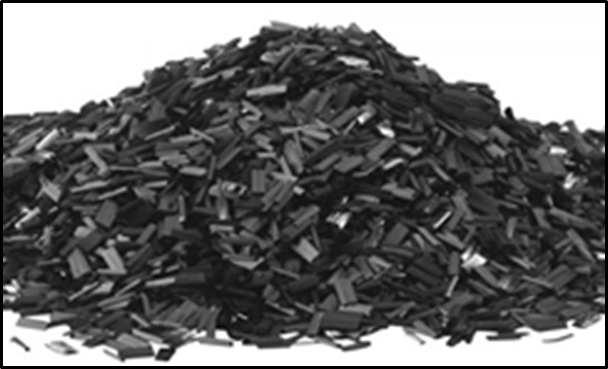
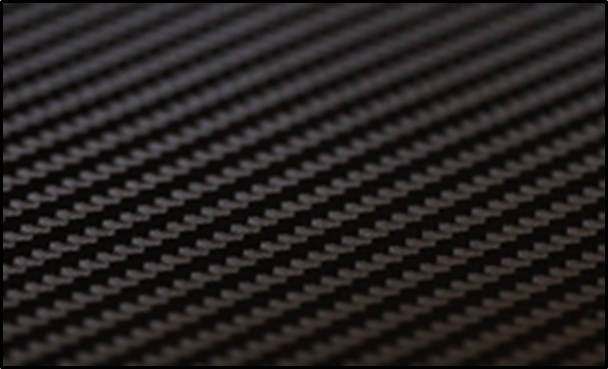
Chopped carbon nanofiber helps to print normally weaker materials by increasing their strength. Afterwards, the material is mixed with thermoplastics such as nylon, PLA or ABS. The role of carbon nanofiber here is increasing the strength and flexibility of model while enhancing its dimensional stability, surface finish and precision. However, while giving priority to strength of model, carbon nanofiber may oversaturate the material which will result in low quality of the component.
Although chopped carbon nanofiber might be a good option for the production of prototypes and end-use parts, it’s not the first choice while manufacturing metal parts. Since metal parts require higher strength, continuous carbon nanofiber is the method used for their production. Whereas the chopped carbon nanofiber is consisted of little pieces adhered together, continuous carbon nanofiber has the same component but it forms a continuous connection across the loading surfaces of the same part. Thanks to this connection, continuous carbon nanofiber adds extra strength to the material combined durability, which differentiates chopped and continuous carbon nanofibers.
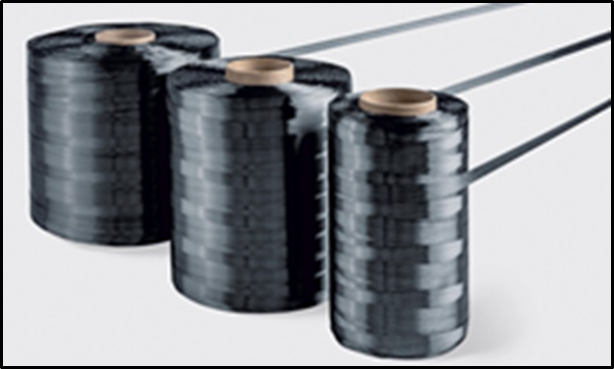
Read more about Carbon Nanofiber:
Comments
Post a Comment