A three roll mill is a machine that uses shear force created by three horizontally positioned rolls rotating in opposite directions and different speeds relative to each other, in order to mix, refine, disperse, or homogenize viscous materials fed into it.
The three-roll mill has proven to be the most successful of the range of roll mills which saw extensive development in the 19th century.
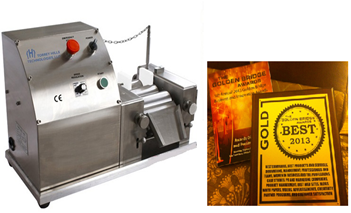
You can see the working mechanism of a three roll mill below:
Three Roll Mills Machine is consisting of three horizontal rollers which rotate opposite direction from the adjacent one with different speeds. Very small gaps between rolls create huge shear force which can produce finely dispersed, mixed and homogenized viscous substances. The material is poured between feeder roll and center roll and then with high shear force material moves through apron roll. The apron part collects the processed mixture from apron roll by the help of a blade. Following shape is illustrating the movement of the substance through the rollers. Until perfectly dispersed material obtained, three roll milling cycles can be performed many times.
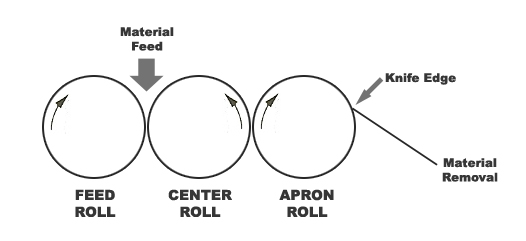
Three Roll Mills is consisting from machine base, cover and roller bearing, Teflon endplates, collecting blade, cooling system, gears and wheels. Six bearing bases for high speed, medium speed and low speed roller exist in the machine. Medium speed roller is fixed to the base and cover while fast and slow rollers can move horizontally to reach desired grinding fineness. The apron can be made up from either steel or Teflon materials. There is also cooling system through the rollers. Inlet and outlet parts on the machine provide the movement of either cooling water or heating liquid such as hot oil to enhance the process quality of substances. The physical structure of the machine can be seen in the following image.
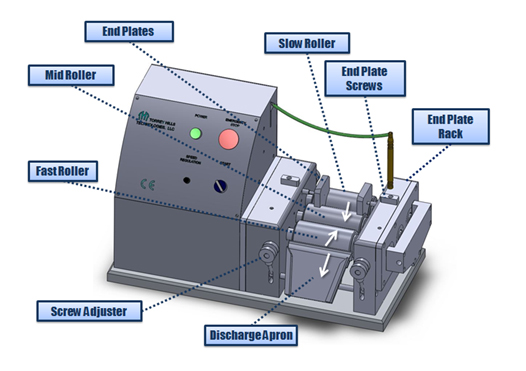
Three roll mills are widely used to mix printing inks, electronic thick film inks, high performance ceramics, cosmetics, plastisols, carbon/graphite, paints, pharmaceuticals, chemicals, glass coatings, dental composites, pigment, coatings, adhesives, sealants, and foods. With the recent development in technology, three roll mills also utilized in the production of cable cover, electronics, soap, and artificial plastics.
Small bench models are used for bench-top development work, laboratory work, and low volume production. Larger bench and floor models are built to meet different production needs from pilot plants to large volume productions.
Particular advantages of using a three roll mill are that it allows high-viscosity pastes to be milled, and that the high surface contact with the cooled rollers allow the temperature to remain low despite the high amount of dispersion work being put in.
You can find the special and technical properties of our three roll mills lab model product:
Special Properties
- Three Roll Mills Lab Model can produce 30 pounds or 3.75 gallons per hour which is higher throughput than most competitors’ model.
- Rolls are made up from 420J2 stainless steel to prevent rust or erosion.
- Rolls are designed for either cooling or heating.
- Rollers are ground to 5um concentricity and 0.5um surface finish for precise applications
- Variable speed control allows adjustable/slower speed runs
- For safety usage, emergency pull cord on top of the machine and stop/start buttons are placed on easily accessible part of the machine
- Roller spacing can be controlled manually with four small hand wheels.
- Easily adjustable Teflon end plates
Technical Properties
Parameters | ||
Roller Material | Stainless Steel | |
Diameter of Roller | 2.5” (65mm) | |
Length of Roller | 5.0” (127mm) | |
Roller Speed Ratio (Fixed) | 1:2:4 | |
Speed of Roller (RPM) | Feed Roller | 0-108 |
Center Roller | 0-216 | |
Apron Roller | 0-432 | |
Motor Power | 3/4HP / .55kW | |
Weight | 165 lbs (75kg) | |
Dimensions | 25”x11”x15” (635mmx280mmx381mm) |
You may give order of three roll mill from the link given below:
Comments
Post a Comment