Silicon Nitride Coating - stoichiometric trisilicon tetranitride (Si3N4) thanks to its very high mechanical and thermal stability is used for tools such as roller bearings used under harsh conditions. In the semiconductor industry, silicon nitride layers are used as dielectric material, passivation layers or can act as hardmask mask. Silicon Nitride has good high temperature strength, creep resistance and oxidation resistance. Silicon Nitride's low thermal expansion coefficient gives good thermal shock resistance. Silicon Nitride is produced in three main types; Reaction Bonded Silicon Nitride (RBSN), Hot Pressed Silicon Nitride (HPSN) and Sintered Silicon Nitride (SSN).
There are two main depositions of silicon nitride layers:
LPCVD Silicon Nitride – Low pressure chemical vapor deposition silicon nitride. LPCVD silicon nitride layers are easily deposited on silicon wafers in a reproducible, pure and uniform way. This leads to silicon nitride layers with low electrical conductivity, very good coverage of edges and high thermal stability. SiNx layers realized by the low pressure chemical vapour deposition (LPCVD) technique typically shows a lower H-content and higher stability against HF.
PECVD Silicon Nitride - plasma enhanced chemical vapour deposition silicon nitride.PECVD silicon nitride layers allow higher growth rate, which therefore leads to thicker layers. Stoichiometry and stress can also be adjusted. High thickness uniformity and etch rates are eventually obtained. PECVD Silicon nitride wafers are particularly suitable for passivation layers. SiNx layers realized by the plasma enhanced chemical vapour deposition (PECVD) technique from SiH4 and NH3 typically – depending on the deposition temperature and gas composition – contain 5 - 20 atom% hydrogen which saturates dangling bonds and thus chemically and mechanically stabilizes the SiNx lattice.
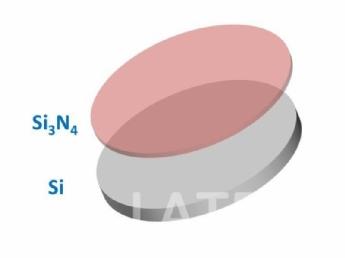
For semiconductor devices, the chemical, electrical and optical properties of amorphous hydrogenated silicon nitride (SiNx) make this material well-suited for different applications, such as for
- passivation or insulating layers in integrated circuits
- masking or etch stop material in wet and plasma etching processes due to its high chemical stability
- masking material in silicon oxidation processes due to the very low oxygen diffusion coefficient in SiNx
- anti-reflective coating in photovoltaics due to its adjustable refractive index
- Another applications:
- Silicon Nitride (SiNx) wafers are used in MEMS devices
- Silicon Nitride (SiNx) wafers are used in Passivation/Barrier film
- Silicon Nitride (SiNx) wafers are used in Integrated circuits (IC)
- Silicon Nitride (SiNx) wafers are used in Hard mask for wet and dry etching
- Silicon Nitride (SiNx) wafers are used in Micro-mechanics.
Comments
Post a Comment